The cable heat pressure test is crucial in ensuring the durability and efficacy of cables, particularly those used in harsh environments. With years of experience in quality assurance for electrical components, I have seen firsthand how vital these tests are.
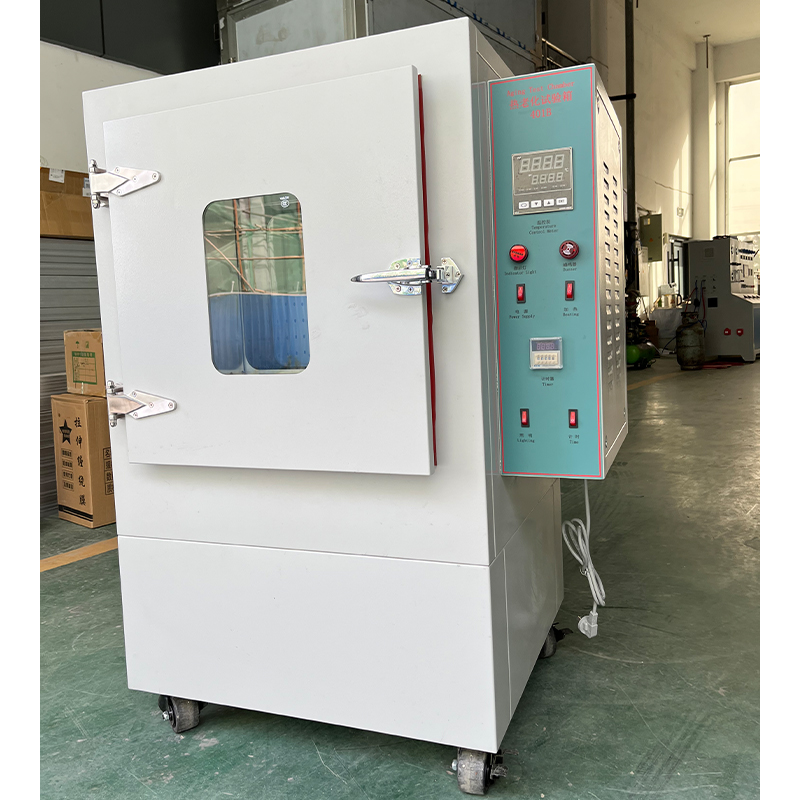
The process of cable heat pressure testing begins with the preparation of the cable samples. These cables are typically subjected to environments that simulate their intended operational conditions. The primary objective is to evaluate how well a cable can withstand extreme heat coupled with varying degrees of pressure. Many industries, including automotive, telecommunications, and industrial manufacturing, rely heavily on these tests to determine cable performance and reliability.
In our laboratory,
precision is paramount. A standardized testing methodology helps ensure consistent results. The testing condition typically involves subjecting the cable to elevated temperatures, sometimes exceeding 90 degrees Celsius, while maintaining specific pressure conditions. This procedure is not merely a regulatory requirement but a testament to the cable manufacturer's commitment to quality and durability.
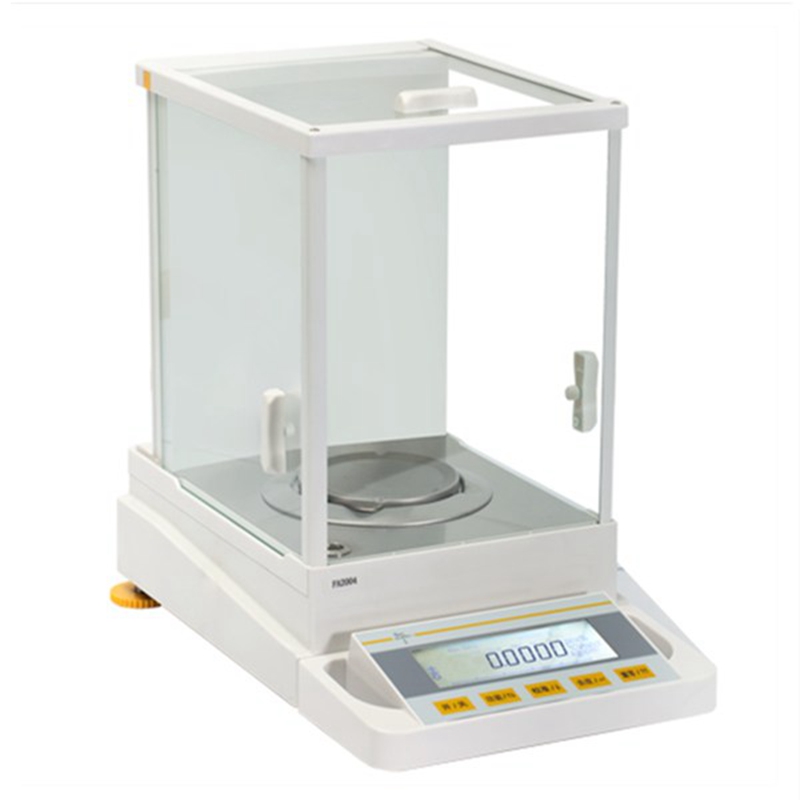
When performing a cable heat pressure test, one must consider the material composition of the cable. Many modern cables are crafted from composite materials, including thermoplastics and elastomers, known for their ability to withstand significant thermal and mechanical stress. An expert's understanding of these materials' properties is essential for interpreting the test results accurately.
The success of a cable in these tests often hinges on the integrity of its insulation. Insulation materials must resist thermal degradation and maintain their structural integrity under pressure. During testing, we observe any instances of deformation, melting, or electrical failure. A thorough analysis of these signs can provide insights into the long-term reliability of the cable.
cable heat pressure test
In addition to the physical and thermal tests, we also incorporate advanced diagnostic tools, such as infrared thermography and digital pressure sensors, to enhance the accuracy of our assessments. These technologies allow us to detect minute changes that might not be visible to the naked eye, providing a more comprehensive understanding of the cable's performance.
Establishing a sense of trust with clients is crucial, and maintaining transparency about our testing methodologies is part of that. Our laboratory adheres strictly to international standards, such as IEC and IEEE guidelines. These standards serve as a foundation for credibility, assuring clients of the reliability of our test results.
Moreover, real-world application of these cables often presents challenges not easily replicated in a controlled environment. Hence, our team continues to gather empirical data through field tests, ensuring our laboratory test results align with actual performance.
In conclusion, the cable heat pressure test is a meticulous procedure that demands both expertise and meticulous attention to detail. By conducting rigorous testing and providing standardized reporting, we aim to empower our clients with reliable data that informs their decision-making processes. As the demand for robust and durable cables continues to grow, the heat pressure test remains a critical indicator of a cable's suitability for application, ensuring safety, reliability, and performance efficiency across all sectors.