Insulation resistance testers play a critical role in maintaining electrical safety and efficiency, especially in industrial and commercial settings. They are indispensable tools for electricians, engineers, and maintenance teams who require accurate measurements of insulation resistance to prevent electrical accidents and failures. This article explores the intricacies of insulation resistance testers, drawing on expert insights and real-world applications to highlight their importance and efficacy.
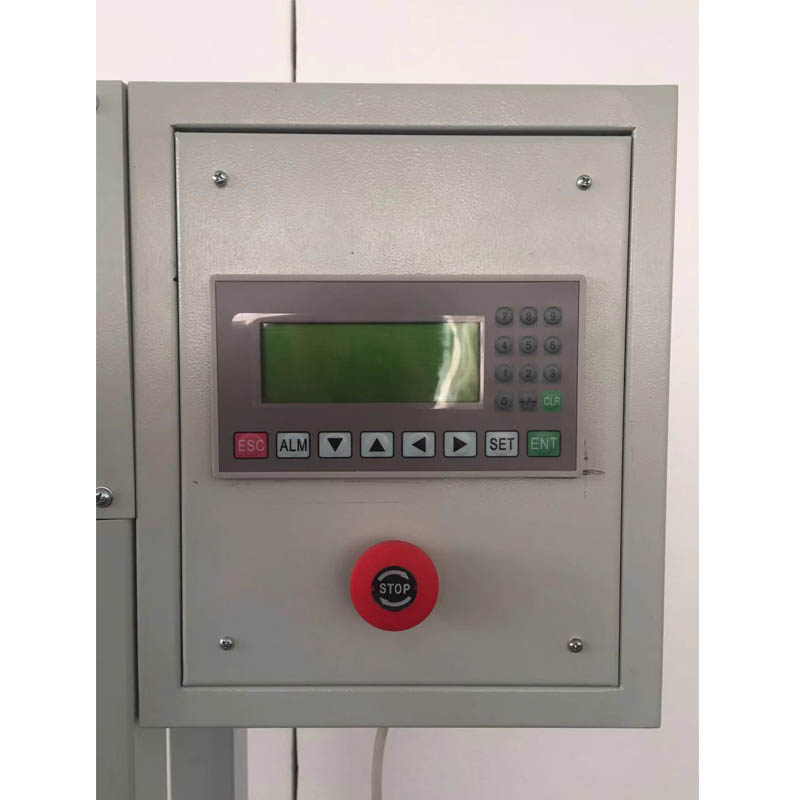
Insulation resistance testers function by applying a high DC voltage through an electrical circuit and measuring the resistance that the electrical insulating materials provide against this electrical flow. A material with high resistance indicates good insulation, while low resistance could signal deteriorated insulation or potential electrical hazards, making maintenance and inspections a priority.
Experts in electrical engineering often prefer brands such as Megger, Fluke, and Kyoritsu due to their reliability and precision. These brands are renowned for crafting highly durable testers that can withstand harsh environments, ensuring longevity and accurate performance over time. Professionals assert that investing in high-quality testers from reputable manufacturers is crucial since safety and precision cannot be compromised.
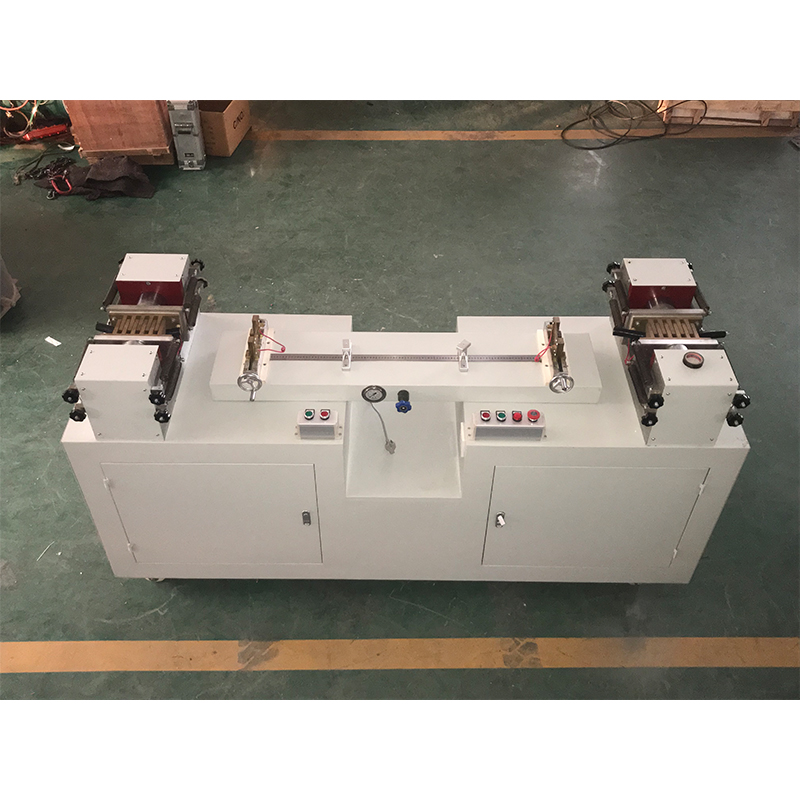
For those new to using insulation resistance testers, it’s essential to develop a foundational understanding of how to interpret test results. Typically, the tester will display a value in megaohms (MΩ), and understanding what constitutes a 'safe' or 'unsafe' reading is key. For example, a reading of thousands of megaohms is generally safe, whereas significantly lower readings prompt further analysis or immediate action.
insulation resistance testers
Design and ergonomics are also important factors to consider when selecting an insulation resistance tester. Experienced users look for devices that are user-friendly, with intuitive interfaces and manageable weight for comfortable handling during prolonged usage. Additionally, modern testers often come with features such as digital displays, automatic calculation capabilities, and voltage warning indicators, which enhance safety and ease of use.
Calibration and maintenance significantly influence the trustworthiness of the readings from insulation resistance testers. Regular calibration, following the manufacturer’s guidelines, ensures the tester delivers accurate readings, reinforcing safety protocols in electrical systems. Professionals advise incorporating test equipment as part of routine maintenance schedules to uphold the highest safety standards.
Real-world applications and feedback from industry practitioners emphasize the significance of insulation resistance testers in a variety of scenarios. For instance, in predictive maintenance, identifying deteriorating insulation early can prevent costly downtime and avert serious electrical faults. Industries such as energy, shipping, and manufacturing rely on these testers to uphold operational integrity and safety.
In conclusion, insulation resistance testers are fundamental in safeguarding electrical infrastructures by accurately assessing insulation effectiveness. Expertise in their use, regular calibration, and selecting the right tools for specific applications are key to leveraging their full capabilities. By integrating these practices and tools, organizations can maintain high safety standards, improve system reliability, and foster trust within their operational ecosystems. As technological advances continue to enhance these devices, insulation resistance testers will remain a cornerstone of electrical safety and performance assessments for years to come.