Selecting the right clamps for tensile testers is critical in achieving accurate and reliable testing results, indispensable for industries relying on material performance insights. Tensile testers, renowned for assessing material strength, ductility, and elastic properties, require just the right set of clamps to hold specimen material firmly in place. The intricacies of selecting these clamps can determine the success of the tests conducted.
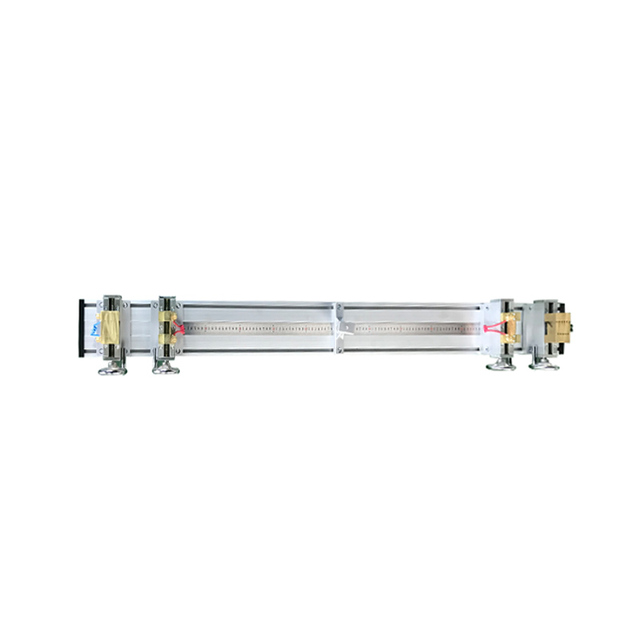
Firsthand experience shows that the clamp's function is not just about holding the sample, but ensuring it remains unaltered under stress. A seasoned material testing engineer shares that the choice of clamp must align with the material type, shape, and size of the specimen. For metals and hard plastics, wedge action grips are preferred for their robust holding power. Meanwhile, pneumatic or hydraulic grips are beneficial for materials that might be sensitive to pressure changes, such as certain polymers and textiles.
Expertise in the field suggests that neglecting to match the correct clamp to material properties can lead to slippage or jaw breaks during testing.
This mishap compromises the authenticity of the test results. Therefore, it is essential to evaluate the clamping force capability and the jaw face size for every unique testing requirement. Testing facilities underline the importance of calibrating these aspects in line with International Standards, such as ASTM and ISO, to maintain consistency and reliability in data collected.
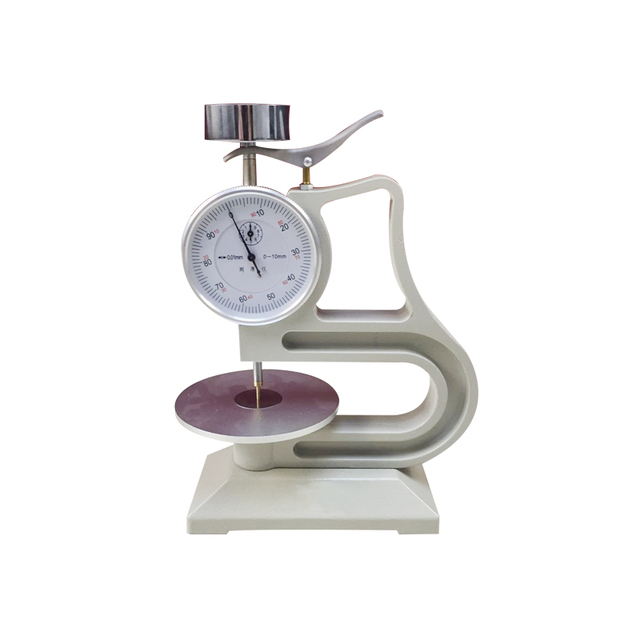
An authoritative voice in tensile testing equipment comments that technology in clamp design has evolved significantly. New-age clamps now offer interchangeable jaw faces, widening the scope of testing across various materials without the need for multiple testers. These advancements have not only increased testing efficiency but also enabled more detailed insights into material behaviors under tension.
For those seeking credibility in their testing processes, trustworthiness is enhanced by investing in clamps that promise durability and precision. This includes utilizing materials such as high-strength steel and advanced composites for jaw construction, which withstands repeated high-pressure testing cycles without distortion. Manufacturers emphasize the rigorous quality checks these clamps undergo to meet global operational standards.
clamps for tensile testers
Furthermore, the implementation of digital interface add-ons for modern clamps has provided unprecedented control over testing processes. Embedded sensors and feedback systems now allow real-time monitoring of clamping force and detect potential errors that could invalidate results, a feature highly favored by experts for maintaining data integrity throughout testing sequences.
In practice, a testing lab encountered frequent errors due to inconsistent clamping forces across different tensile tests. By upgrading to smart clamps integrated with force feedback technology, they reported a remarkable reduction in testing errors, resulting in substantial improvements in data reliability.
Finally, professional insights draw attention to the maintenance of these clamps, which is often overlooked. Regular cleaning, calibration, and inspection are integral for extending the service life and maintaining optimal performance, ultimately safeguarding the investment and ensuring consistent test outcomes.
Understanding the intricacies of choosing, using, and maintaining clamps for tensile testers is a decisive factor for any industry reliant on material testing. As the landscape of material science and testing machinery advances, staying informed and adapting to innovative solutions will confer a significant edge in achieving precise and reliable testing outputs.