In the rapidly evolving world of electrical engineering and manufacturing, the precision and reliability of custom wire and cable assemblies can significantly impact performance outcomes. Custom wire and cable testing machines play a pivotal role in ensuring the reliability and efficiency of cable systems, serving industries such as telecommunications, automotive, aerospace, and consumer electronics. Understanding the nuances of these sophisticated machines is essential for any company looking to enhance its production capabilities while maintaining high-quality standards.

Custom wire and cable testing machines are designed to assess various aspects of wire and cable assemblies, including their mechanical integrity, electrical performance, and environmental resistance. These critical machines support the entire life cycle of cable products, from design validation to production testing and final quality assurance.
One of the primary attributes of these machines is their ability to conduct comprehensive testing regimes that ensure compliance with industry standards such as UL, ISO, and IEC. These standards set rigorous benchmarks for aspects like tensile strength, insulation resistance, electrical continuity, and voltage withstand capabilities. Advanced testing machines simulate real-world conditions, providing essential data that can be used to improve both design and manufacturing processes.
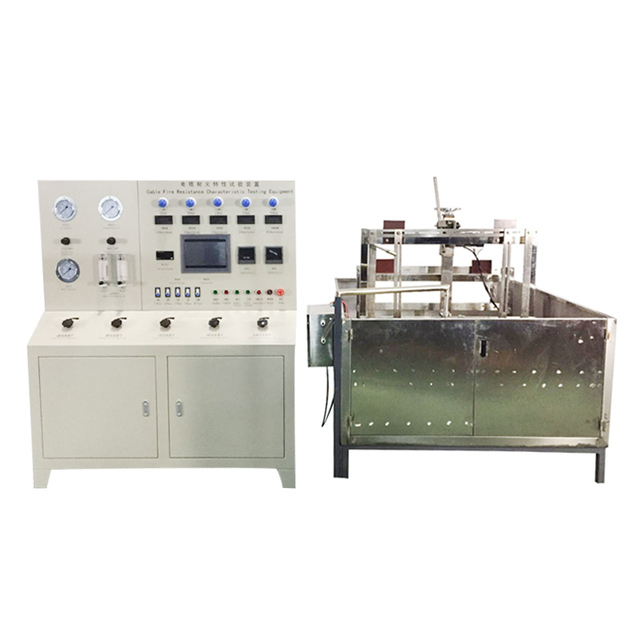
Experience plays a crucial role in the successful deployment and utilization of wire and cable testing machines. Manufacturers with years of experience are able to customize testing equipment to meet specific project demands, whether that involves unique voltage requirements, unusual environmental conditions, or proprietary connector configurations. These customized solutions often incorporate the latest technology in automation and data analysis, allowing for rapid testing cycles and accurate feedback loops that improve both process efficiency and product quality.
Expertise in the field of wire and cable testing requires a deep understanding of both the electrical properties of materials and the mechanical forces at play during cable assembly and installation. Advanced testing machines are equipped with state-of-the-art sensors and control systems that provide highly precise measurements. By leveraging sophisticated software, operators can conduct complex analyses such as impedance measurements, high-frequency transmission tests, and dynamic stress testing, which are essential for ensuring that cables will perform well under varying conditions.
custom wire and cable testing machine
Authoritiveness in this sector is characterized by adherence to the highest levels of industry standards and regulations, backed by the certification from recognized bodies. Leading manufacturers of wire and cable testing machines often collaborate with industry consortia to help shape emerging standards and drive innovation in testing methodologies. These companies routinely lead workshops, publish research papers, and offer training programs to disseminate best practices and technological advancements to a broad audience of engineers and technicians.
The trustworthiness of these machines is demonstrated through their consistent performance and the reliability of their test results. A trusted wire and cable testing provider will offer robust customer support, including installation, calibration, maintenance, and even custom-tailored training programs for client personnel. This ensures that machines continue to operate optimally, providing dependable data over long-term use.
Investing in advanced wire and cable testing equipment can result in substantial benefits for manufacturing operations. By reducing downtime associated with faulty cable assemblies, manufacturers can enhance their overall productivity. High-accuracy testing can also reduce warranty claims and increase customer confidence, as end-users rely on the assurance that tested products meet or exceed specified performance criteria.
Additionally, these machines can facilitate rapid product innovation. By enabling more thorough testing during the design phase, companies can bring new cable products to market faster while ensuring they are robust and reliable. This speed-to-market advantage is particularly crucial in competitive industries where technological advancements frequently dictate market leadership.
In conclusion, custom wire and cable testing machines are indispensable tools in modern manufacturing, providing essential insights that drive quality and reliability. By understanding their capabilities and leveraging their advanced features, companies can not only enhance their operations but also foster a culture of innovation that positions them well in a rapidly evolving marketplace. Choosing a reputable provider with a track record of excellence in the field can ensure that your investment delivers substantial returns in terms of both efficiency and credibility.